About the Manual Packing Industry
This sector does not get the same attention as the automated counterpart, as its humble processes seem so simple and ordinary. But manual packing remains a vital part of the packaging industry, delivering results that robots and automation currently cannot achieve. Outside of the factories that mass-produce commodities, there remains a steady flow of products that are best suited to the expert touch of a human. Two common factors are seen:
- Small batches – a human packer can learn a new packing task in seconds, no programming or modification of machinery is needed. The massively-growing industry of tiny batches is ecommerce, and fulfilment centres depend on rapid handling of thousands of unique customer orders.
- Delicate items – although modern robots can achieve sensitive handling beyond humans, they have to be specially designed for this, and frequently this is not cost-effective. A manual worker can handle all manner of delicate objects easily, and can also perform the task of final quality-control at the same time as packing.
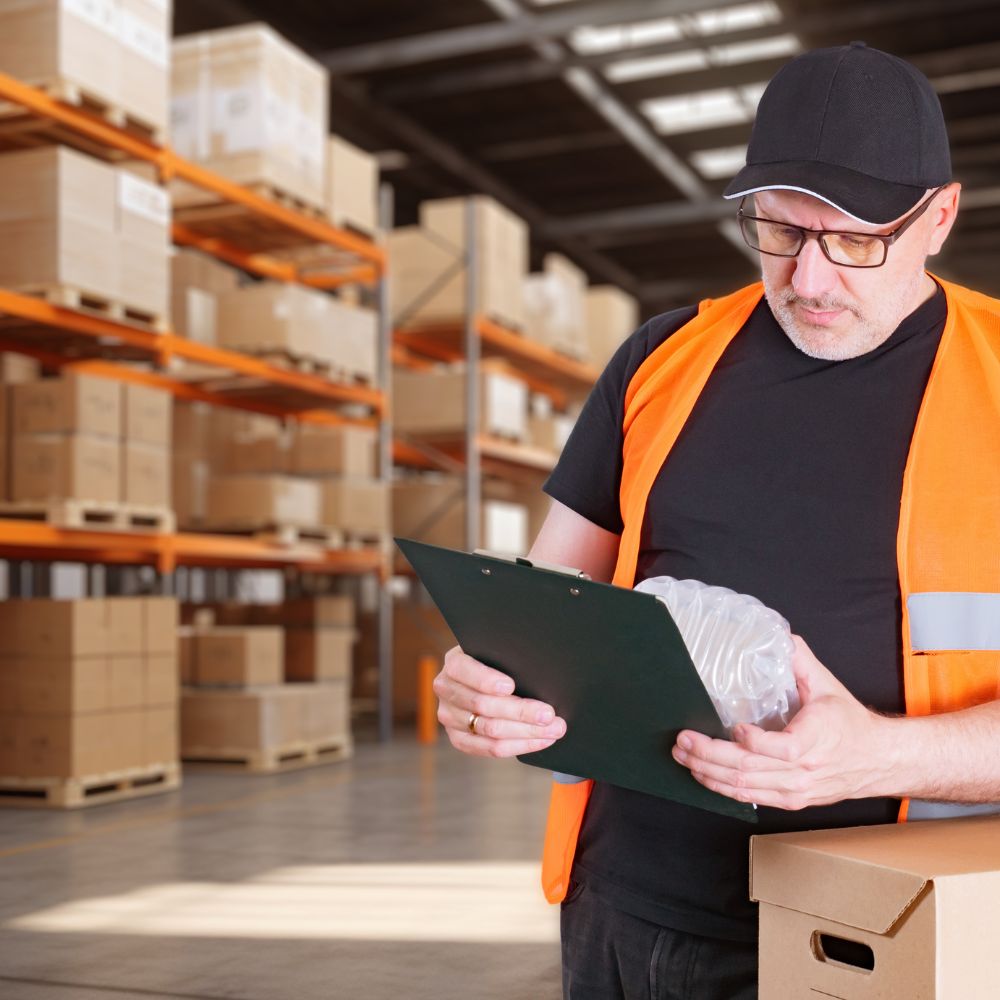
Particular Challenges in Manual Packing
In the constant drive for improved efficiency and competitiveness, the process of manual packing has obvious challenges. With the ever-present danger of work being out-sourced to countries with a lower cost of labour, businesses in the UK are innovating to keep their manual-packing workforce relevant and productive. Also, new technologies have not changed the average length of a human arm from 63.5cm, nor made it possible to work continuously without suffering strain. Consequently, any significant advances that are made, are by improving the environment they work in, and streamlining processes. This is where high-tech materials and products complement the low-tech operation, keeping the task competitive. Recently we witnessed two examples where a high-performance polymer work surface helped improve a manual packing operation.
Flat-pack furniture Distribution
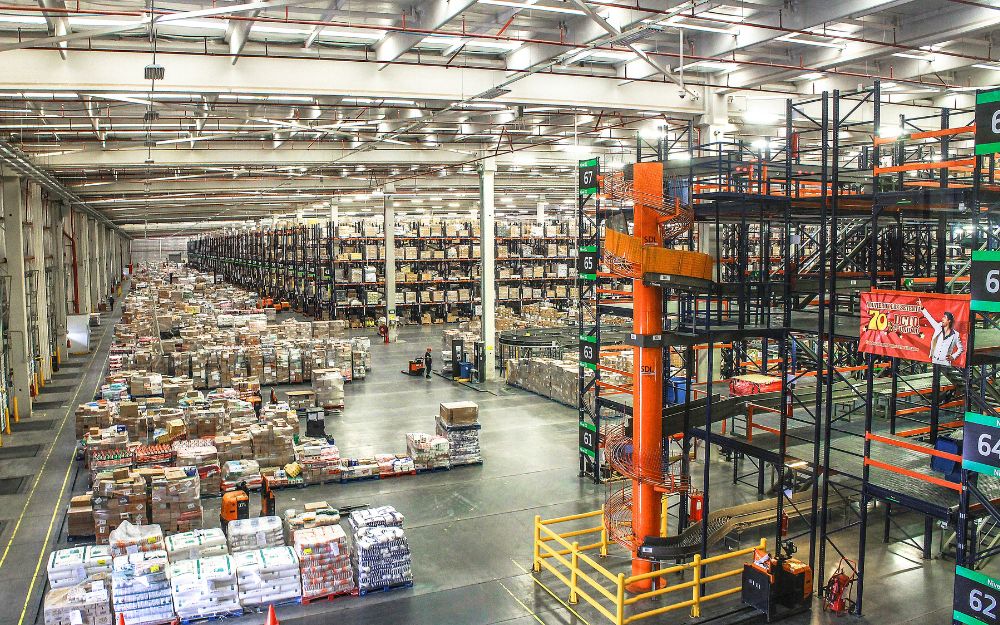
A UK distribution leader landed the contract for a global furniture brand and invested heavily in packing workstations. Although automation was relevant for some tasks, some of the processes could only be done by hand. To achieve maximum efficiency, special workstations were designed, with surfaces at the ideal height and angle for manual packing, and apertures cut in the tabletop to facilitate parts bins and packing tools or machines. A top priority of this process was to pack and despatch with zero damage – the cost of returns and dis-satisfied customers was high. Furniture can be heavy to handle and landing it down too hard on the packing table was all too easy. A cost-effective workforce might have a widely diverging skillset, and an environment that could cope with numerous different operators was looked for. The final packing process would likely involve cutting with knives or rotary cutters, and safety with cutting was important.
This customer needed a work-surface which could meet key criteria:
- Must be soft but durable to cushion knocks but stand up to wear
- Must be self-healing to make cutting safer and survive multiple cuts
- Must be cut to a special size with holes cut to suit apertures in the workstation
The Rhino Heavy Duty mat was chosen, for it soft but tough surface, with a low-friction light texture which helps slide heavy items easily. And the self-healing properties made handling regular cutting a dream. Furthermore, it can be easily CNC cut making fully customised work surfaces a practical reality.
Luxury Cars Parts Packed for Distribution and Export
Another case we were called to recently involved the handling of luxury car parts. The company was packing for export high-value car parts that had just left the factory. This specialised business handled unique customer requests for export, and worked beside the manufacturer in the midlands, providing a rapid shipping service. In some cases, dismantling entire vehicles was required to fulfil the order, and some of these parts had not long left the spray shop of the production line. The high-gloss painted body parts needed very careful handling, but at top speed and efficiency. The ideal solution again was the Rhino Heavy Duty mat where its 4.5mm thickness would stand up to the strain, and the relatively soft Shore hardness of 50 would cushion delicate car panels. Large cars have large parts and need large workbenches – this was another reason for suggesting the Heavy Duty mat, as it is available in single unjoined pieces up to 3.6 x 1.8m, or 4.8m x 1.2m.
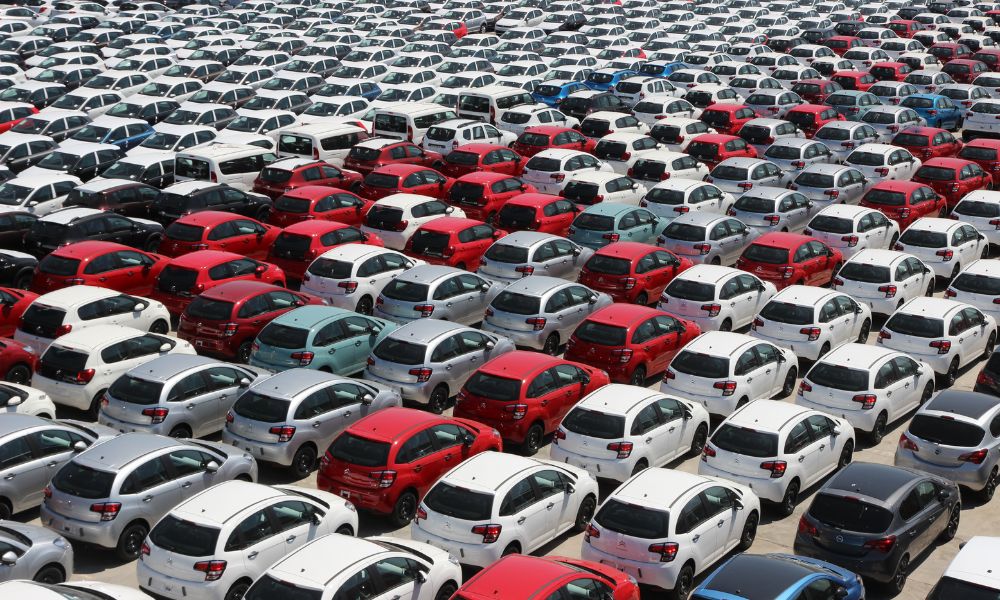
More about the Heavy Duty Cutting Mat
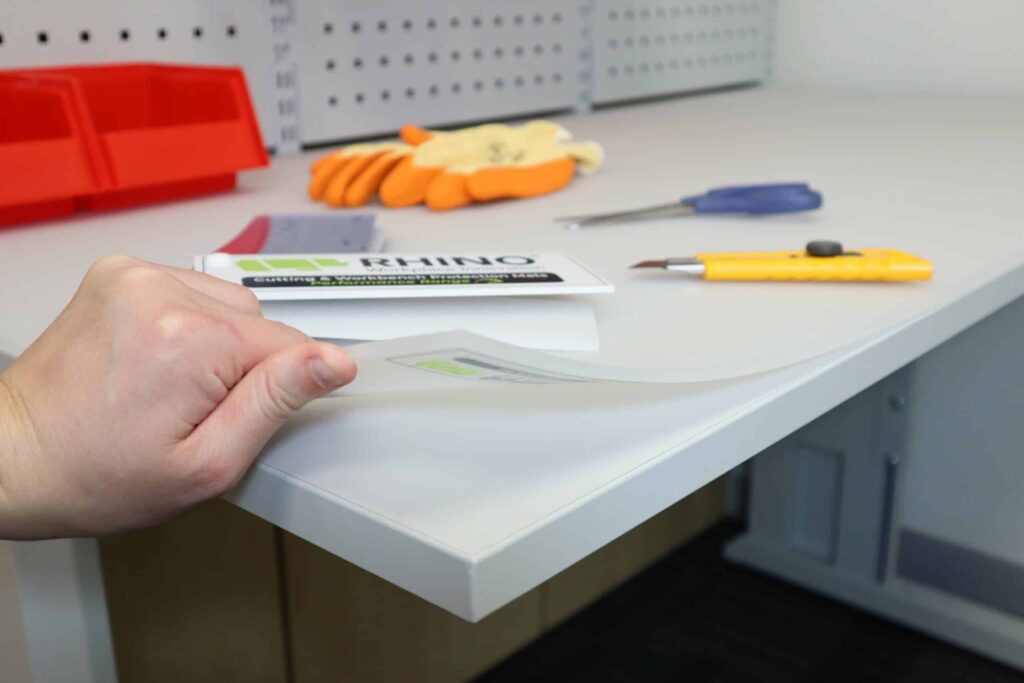
Made from a modern polymer that combines a number of properties, the Rhino Heavy Duty mat was developed to bring maximum performance to mid-range price projects. Like all Rhino cutting mats, it is a self-healing product, which means that the surface is excellent for cutting on. It is made in a single layer, which avoids the issues of fragmentation that occur in multi-layer cutting mats. It is available in a variety of standard sizes, but is also frequently cut to size, or cut to intricate shapes with a CNC router. Order the Rhino Heavy Duty mat online today, or request a free sample pack for evaluation.