Discover expert workbench maintenance tips to boost durability, reduce wear, and ensure long-term performance in DIY and industrial workspaces.
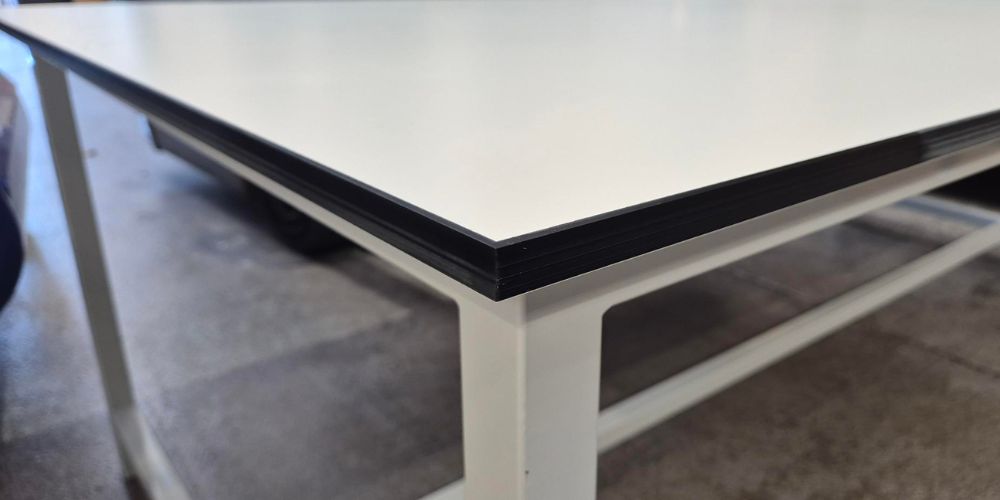
Extend Workbench Lifespan: Maintenance Tips for Durability & Care
In any professional workshop or industrial environment, the workbench is more than just a surface; it’s the backbone of productivity. From heavy-duty assembly tasks to precision cutting, a well-maintained bench directly affects safety, efficiency and long-term performance. Yet, despite its importance, workbench maintenance is often overlooked until problems arise.
Keeping your bench in top condition not only reduces wear and tear but also helps extend its usable life. This means fewer disruptions, lower repair costs and improved workflow. Whether you’re managing a high-output facility or a compact garage setup, proper industrial bench care supports smoother operations and better results.
At Rhino Cutting Mats, we understand the importance of durable, well-maintained workstations. While we specialise in heavy duty cutting mats and workshop solutions, we also help professionals get more from their setup through reliable, long-lasting gear and maintenance insights.
In this guide, we’ll walk through essential steps to improve workbench durability, from daily upkeep to seasonal checks and smart storage strategies.
What Are Anti Static Mats?
Anti static mats, sometimes called ESD or dissipative mats, are specially engineered floor or bench coverings that control static electricity by providing a path to ground. Made from materials with controlled electrical resistance, they prevent build‑up of static charges and eliminate sudden discharges that could damage sensitive equipment.
It’s important to distinguish between:
- Anti‑static mats — engineered to reduce static build‑up.
- ESD mats — designed to manage and safely dissipate electric charges.
- Conductive mats — often used in applications needing rapid charge transfer.
Each type serves a unique purpose; choosing the correct one ensures maximum protection. Rhino’s high‑performance solutions, such as the Rhino Xtratuff ESD Workbench Mat provide clarity and compliance for delicate workspaces.
Why Workbench Maintenance Is Essential?
Even the toughest workbenches are vulnerable to wear over time. Common issues include rust caused by moisture, surface damage from repeated use, chemical stains and loose joints due to heavy vibrations or overloading. For wooden benches, neglect can lead to cracks or warping, while metal benches may suffer from corrosion or joint fatigue.
These problems don’t just affect the appearance of your bench. They can compromise safety, reduce productivity and lead to costly repairs or replacements. An unstable or damaged bench can cause accidents, damage tools and slow down your workflow.
Routine workbench maintenance helps prevent these issues before they become serious. Whether you’re a DIY enthusiast or managing operations on an industrial scale, consistent care keeps your workspace dependable and efficient. Good industrial bench care not only protects your equipment but also helps reduce downtime, extend the lifespan of your bench and save money over time.
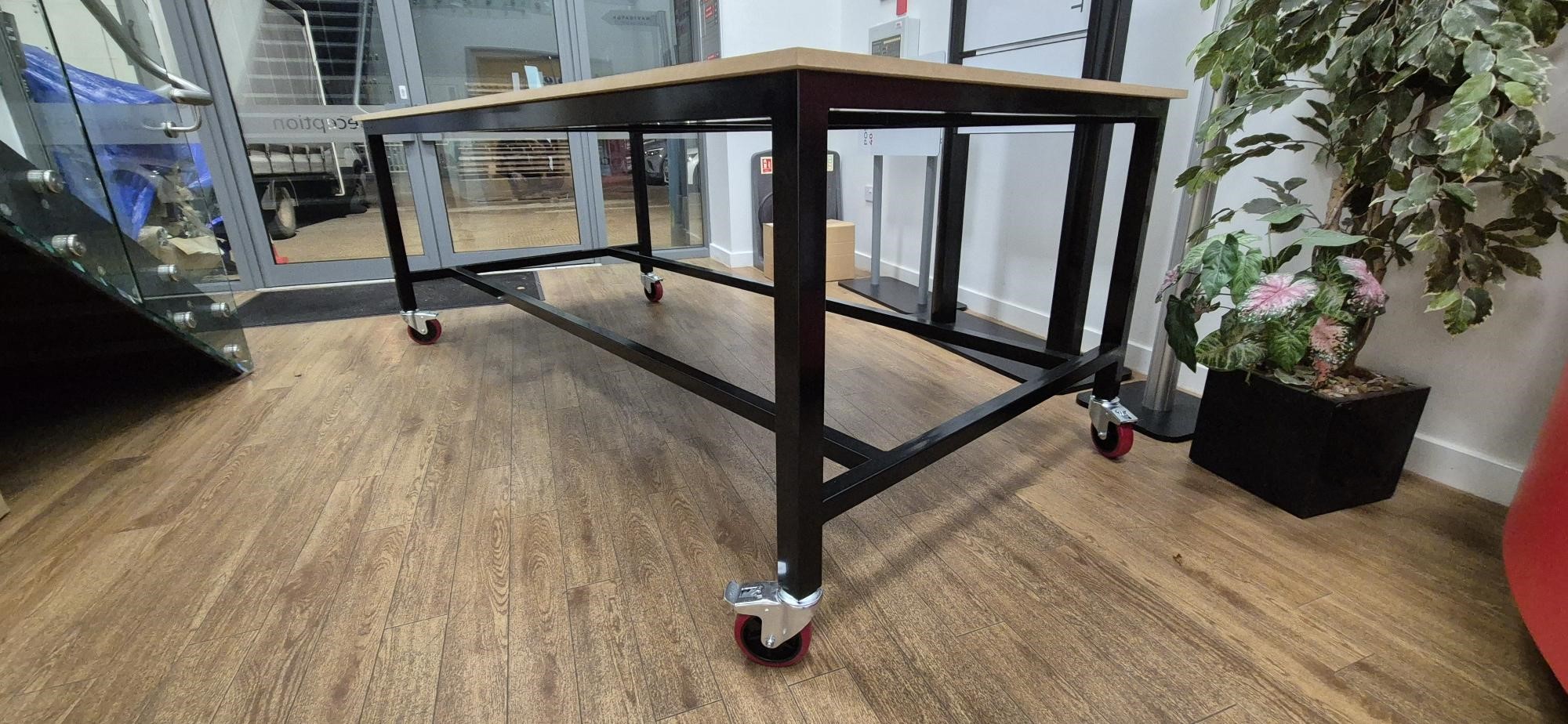
Daily and Weekly Workbench Maintenance Tasks
Routine care is the foundation of effective workbench maintenance. By building simple daily and weekly habits, you can prevent long-term damage and keep your workspace clean, safe and efficient.
Start each day by wiping down all surfaces. Dust, sawdust, metal shavings and spilled liquids can quickly build up, leading to stains, surface wear or corrosion. Use a soft cloth and appropriate cleaning agents based on your bench material. For wooden surfaces, a light application of wiping oil can keep the surface conditioned. For metal benches, apply a light rust protector to exposed areas.
Adding surface protection is another smart habit. Rubber mats or anti-slip liners can shield your bench from tool impacts, chemical spills and scratches. They’re especially useful in industrial settings where heavy use is the norm.
Weekly checks should include a quick inspection of mounted tools and accessories. Tighten any loose bolts or screws, check for wear on vices or clamps, and make sure tools are returned to their correct positions. This helps prevent damage to both the bench and the tools themselves.
These simple daily and weekly steps go a long way toward maintaining a reliable and durable workbench for any level of use.
Monthly and Seasonal Industrial Bench Care Routines
While daily cleaning keeps your workbench presentable, monthly and seasonal routines are essential for long-term performance and structural integrity. This deeper level of industrial bench care helps identify and fix issues before they lead to failures or safety hazards.
Begin with a full inspection of the bench frame. Check joints, welds, brackets and fasteners for any signs of stress, movement or cracking. If your bench includes adjustable legs or modular features, test for stability and levelness. Any wobbling or uneven weight distribution should be addressed immediately to avoid structural fatigue.
Next, tighten all hardware including bolts, screws and locking mechanisms. Over time, vibration from tools and heavy use can loosen components. Realign any skewed parts and pay close attention to mounted vices or clamp areas, which often bear repeated pressure. If you use vices frequently, clean and lubricate the threads to keep them moving smoothly.
For benches with moving parts such as hinged shelves, foldable legs or sliding drawers, apply lubricant to reduce friction and wear. Use silicone spray or light machine oil depending on the materials involved.
Seasonally, reapply protective coatings suited to your bench type. For wooden benches, a fresh layer of sealant prevents moisture absorption and cracking. For metal benches, apply a rust inhibitor to exposed surfaces, especially in humid or industrial environments.
Finally, check the bench’s weight-bearing capacity against current usage. Industrial workbenches can weaken over time, so verifying load tolerances ensures ongoing safety and performance throughout the year.
Storage and Environmental Control
Where and how you store your workbench play a significant role in its lifespan. Indoor storage is ideal, especially in controlled environments where humidity and temperature fluctuations are minimal. Keeping your bench away from direct sunlight prevents UV damage to wood finishes and composite materials, while shielding it from moisture reduces the risk of corrosion and mould.
Humidity and extreme temperature changes can degrade both wood and metal. Wood may warp, swell or crack, while metal parts are more prone to rust and fatigue. Using dehumidifiers in garages or workshops can help stabilise conditions, especially in damp climates.
Proper bench positioning also matters. Ensure your bench sits on a level surface to distribute weight evenly and prevent structural strain. Ground-level instability can lead to joint stress, uneven tool wear, or even accidents. Simple adjustments like rubber feet or stabilising pads can make a significant difference in maintaining long-term durability and safety.
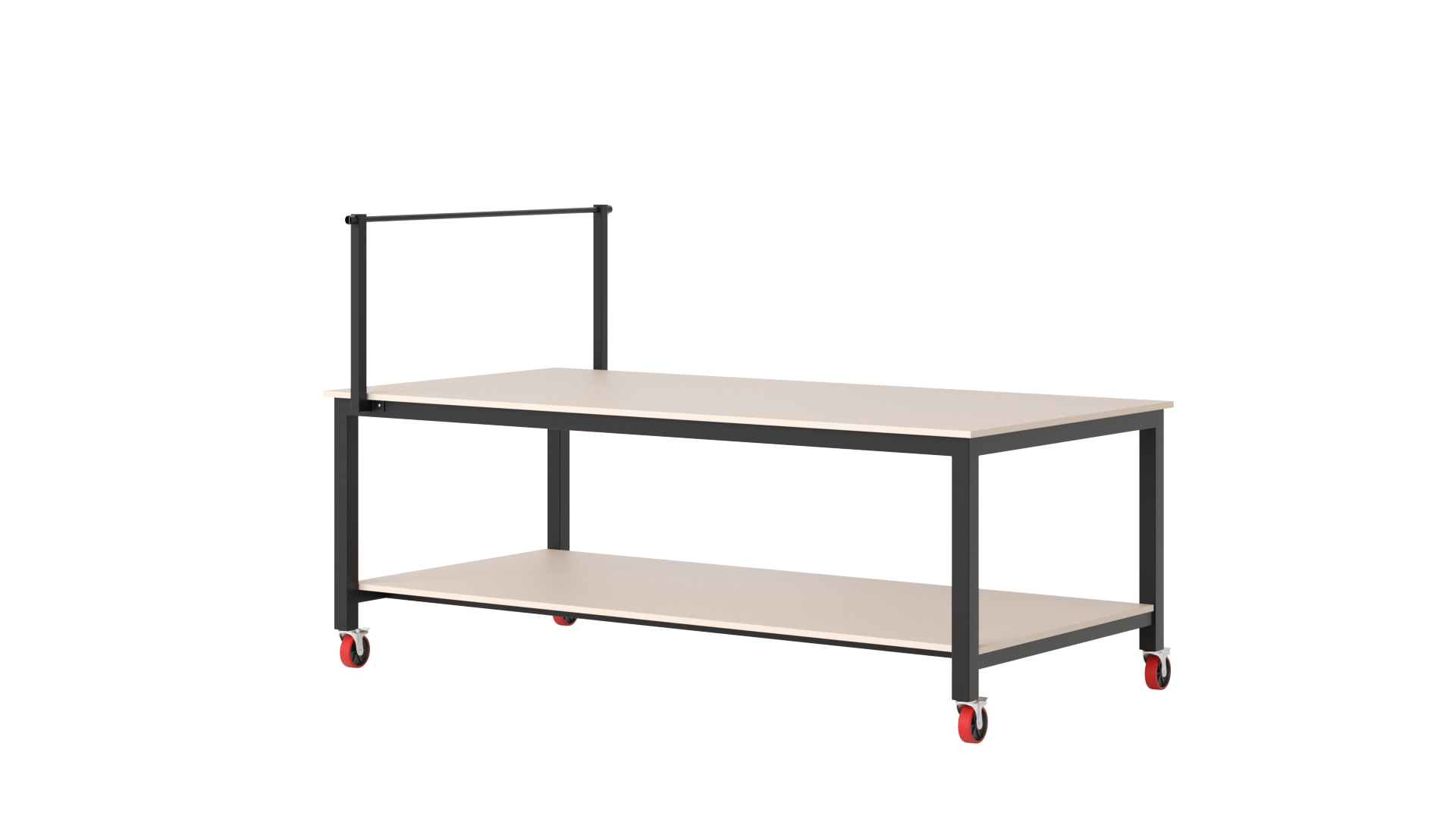
Using the Right Tools and Parts for Maintenance
Effective workbench maintenance isn’t just about routine — it’s about using the right materials and tools for the job. Always opt for manufacturer-recommended or high-quality replacement parts. Original equipment manufacturer (OEM) components ensure compatibility and maintain the integrity of the workbench, while lower-quality aftermarket parts can lead to premature failure.
Use cleaning agents and lubricants that suit your bench material. For example, wood benches benefit from natural oils or specialised sealants, while metal surfaces require rust inhibitors and silicone-based lubricants. Avoid harsh chemicals that can degrade finishes or weaken protective coatings.
Keep a basic maintenance toolkit on hand, including adjustable wrenches, screwdrivers, lubricant sprays, wood oil or sealant and anti-rust treatments. A level and rubber mallet can also help with minor realignments. Using the correct tools not only improves the quality of your maintenance efforts but also extends the lifespan of your bench without unnecessary damage or wear.
Training Staff for Industrial Workbench Care
In shared or industrial workspaces, proper workbench maintenance relies not only on systems but also on people. Establishing clear protocols ensures that every team member understands their role in keeping the bench in working condition. This is especially important in environments where multiple users rely on the same equipment.
Start by creating a simple checklist for daily, weekly and monthly maintenance tasks. Provide hands-on training for tasks such as wiping down surfaces, checking fasteners, applying protective coatings and identifying signs of wear. Make sure team members know which tools and products to use based on the bench materials.
Encouraging staff to report minor issues early can prevent larger, costlier problems down the line. A small crack, wobble or rust spot caught early can often be resolved with minimal effort. Clear communication and accountability help reduce downtime, extend bench life and maintain a safer, more efficient workspace for everyone involved.
Leveraging Technology (for Industrial Settings)
Modern workshops can take industrial bench care a step further by incorporating technology. A CMMS (Computerised Maintenance Management System) helps schedule routine tasks, set reminders and track service history. This is especially useful in larger facilities where manual tracking becomes inefficient.
IoT (Internet of Things) sensors can monitor bench stability, weight loads or even environmental conditions. Alerts can notify staff when maintenance thresholds are reached. Digital logs also provide a clear overview of each bench’s condition, helping managers make informed decisions about repairs or replacements. These tools add precision and reliability to traditional maintenance routines.
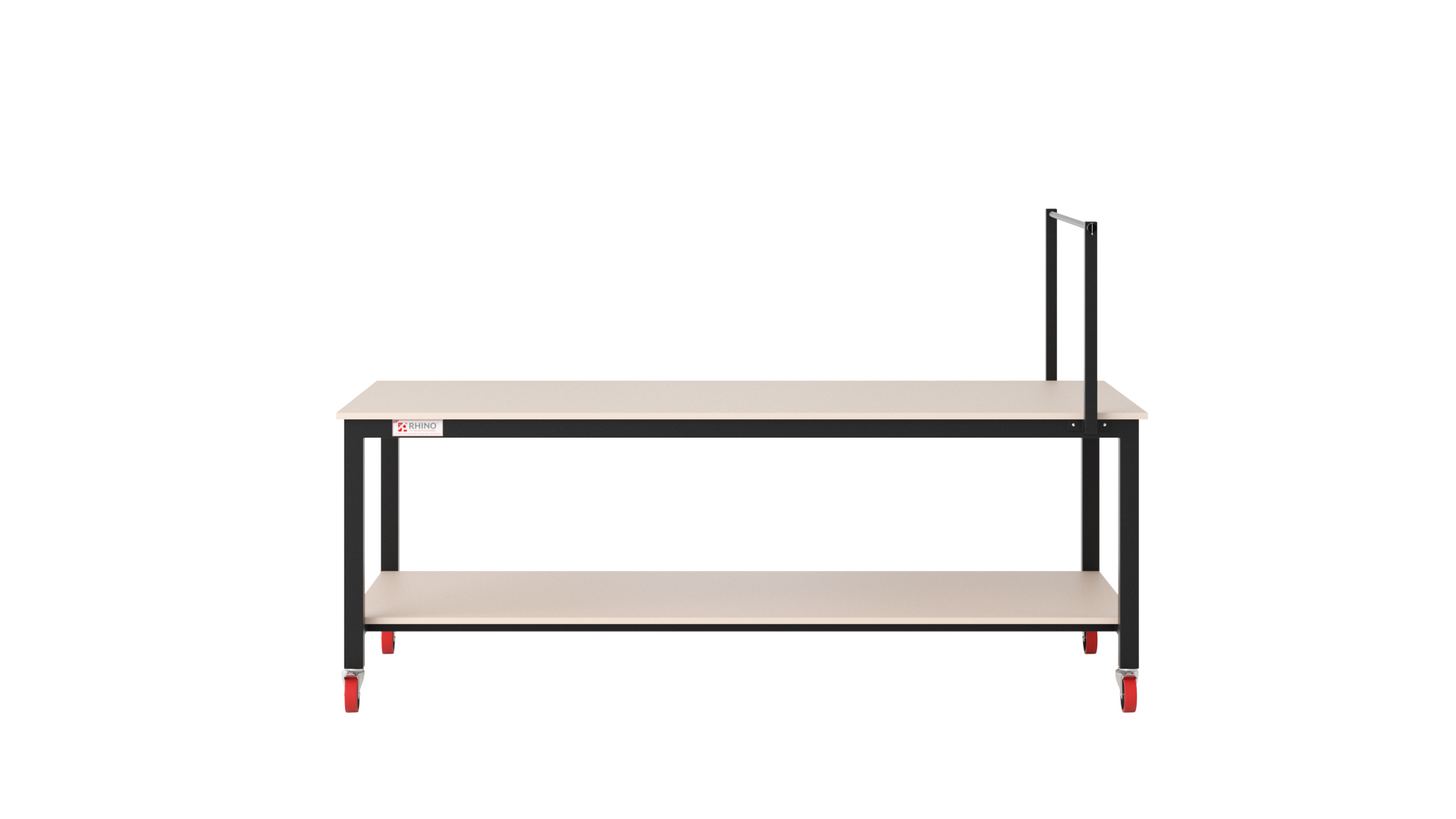
Common Mistakes That Reduce Workbench Lifespan
Modern workshops can take industrial bench care a step further by incorporating technology. A CMMS (Computerised Maintenance Management System) helps schedule routine tasks, set reminders and track service history. This is especially useful in larger facilities where manual tracking becomes inefficient.
IoT (Internet of Things) sensors can monitor bench stability, weight loads or even environmental conditions. Alerts can notify staff when maintenance thresholds are reached. Digital logs also provide a clear overview of each bench’s condition, helping managers make informed decisions about repairs or replacements. These tools add precision and reliability to traditional maintenance routines.
Common Mistakes That Reduce Workbench Lifespan
Neglecting basic care can drastically shorten the life of your workbench. One of the most common errors is overloading beyond the bench’s rated weight capacity, which can weaken joints or cause structural failure. Another is the use of harsh cleaning chemicals without proper surface protection, especially on wood or coated metal.
Minor issues like loose screws, slight warps or small rust spots are often ignored until they become serious problems. These seemingly small oversights can compound over time, leading to costly repairs or replacements. Recognising and addressing these early helps maintain both safety and workbench durability.
Final Thoughts: Improving Workbench Durability Long-Term
Maintaining your workbench doesn’t require complex tools or expensive products — just consistency and attention to detail. By adopting a regular care routine that includes cleaning, inspecting, lubricating, protecting surfaces and training staff, you can extend the life of your bench significantly.
Small efforts like wiping down the surface each day or tightening a loose bolt once a month make a big difference over time. Whether you’re a home DIYer or managing a large facility, these habits ensure your bench remains reliable, safe and cost-effective in the long run.
At Rhino Cutting Mats, we believe a high-quality workspace starts with the right foundations. In addition to supplying premium cutting mats, we support professionals with practical advice to improve industrial bench care and overall workshop performance.
If you want to avoid unnecessary downtime and get the most from your equipment, start implementing these workbench maintenance practices today. A longer-lasting, safer and more productive workspace is within reach.